For the test, an 18,000-pound pallet, simulating
the actual X-38, was dropped from the back of a C-130 aircraft
at an altitude of 21,500 feet. A 28-foot diameter extraction
parachute pulled the test platform from the aircraft at an
air speed of 130 miles per hour to begin the flight test.
Once out of the aircraft, a newly designed 80-foot diameter
drogue parachute stabilized and slowed the platform to a vertical
airspeed of 62 miles per hour and enabled the parafoil to
begin a five-stage deployment process. During its 11-minute
long flight, the parafoil slowed the test pallet to a gentle
vertical landing speed of less than eight miles per hour.
"This parafoil is so big there is no way that it can
all deploy at once," said Brian Anderson, X-38 Project
Manager. "Because of its size, the dynamic forces on
the parachuteís structure are phenomenal." The
size of the parafoil posed technical challenges for the X-38
team. One problem encountered in past tests has been to ensure
that the parachute opens evenly. To solve this and make certain
that the parachute opens symmetrically and rapidly, the team
developed a revolutionary self-sealing floor vent system on
the parafoil's underside. During the recent test, the parafoil
opened to its full size in only 30 seconds. The parafoil was
stitched together at Pioneer Aerospace's facility in Columbia,
MS. Because of its |
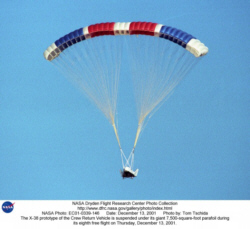 |
Project Description:
The X-38 Crew Return Vehicle (CRV) research project is
designed to develop the technology for a prototype emergency
crew return vehicle, or lifeboat, for the International
Space Station. The project is also intended to develop a
crew return vehicle design that could be modified for other
uses, such as a joint U.S. and international human spacecraft
that could be launched on the French Ariane-5 Booster.
The X-38 project is using available technology and off-the-shelf
equipment to significantly decrease development costs. Original
estimates to develop a capsule-type crew return vehicle
were estimated at more than $2 billion. X-38 project officials
have estimated that development costs for the X-38 concept
will be approximately one quarter of the original estimate.
Off-the-shelf technology is not necessarily "old"
technology. Many of the technologies being used in the X-38
project have never before been applied to a human-flight
spacecraft. For example, the X-38 flight computer is commercial
equipment currently used in aircraft and the flight software
operating system is a commercial system already in use in
many aerospace applications. The video equipment for the
X-38 is existing equipment, some of which has already flown
on the space shuttle for previous NASA experiments. The
X-38's primary navigational equipment, the Inertial Navigation
System/Global Positioning System, is a unit already in use
on Navy fighters. The X-38 electromechanical actuators come
from previous joint NASA, U.S. Air Force, and U.S. Navy
research and development projects. Finally, an existing
special coating developed by NASA will be used on the X-38
thermal tiles to make them more durable than those used
on the space shuttles.
The X-38 itself was an unpiloted lifting body designed
at 80 percent of the size of a projected emergency crew
return vehicle for the International Space Station, although
two later versions were planned at 100 percent of the CRV
size. The X-38 and the actual CRV are patterned after a
lifting-body shape first employed in the Air Force-NASA
X-24 lifting-body project in the early to mid-1970s.
The current vehicle design is base lined with life support
supplies for about nine hours of orbital free flight from
the space station. ItÕs landing will be fully automated
with backup systems which allow the crew to control orientation
in orbit, select a deorbit site, and steer the parafoil,
if necessary. The X-38 vehicles (designated V131, V132,
and V-131R) are 28.5 feet long, 14.5 feet wide, and weigh
approximately 16,000 pounds on average. The vehicles have
a nitrogen-gas-operated attitude control system and a bank
of batteries for internal power. The actual CRV to be flown
in space was expected to be 30 feet long.
The X-38 project is a joint effort between the Johnson
Space Center, Houston, Texas (JSC), Langley Research Center,
Hampton, Virginia (LaRC) and Dryden Flight Research Center,
Edwards, California (DFRC) with the program office located
at JSC. A contract was awarded to Scaled Composites, Inc.,
Mojave, California, for construction of the X-38 test airframes.
The first vehicle was delivered to the JSC in September
1996. The vehicle was fitted with avionics, computer systems
and other hardware at Johnson. A second vehicle was delivered
to JSC in December 1996.
Flight research with the X-38 at Dryden began with an unpiloted
captive-carry flight in which the vehicle remained attached
to its future launch vehicle, DrydenÕs B-52 008.
There were four captive flights in 1997 and three in 1998,
plus the first drop test on March 12, 1998, using the parachutes
and parafoil. Further captive and drop tests occurred in
1999. In March 2000 Vehicle 132 completed its third and
final free flight in the highest, fastest, and longest X-38
flight to date. It was released at an altitude of 39,000
feet and flew freely for 45 seconds, reaching a speed of
over 500 miles per hour before deploying its parachutes
for a landing on Rogers Dry Lakebed.
In the drop tests, the X-38 vehicles have been autonomous
after airlaunch from the B-52. After they deploy the parafoil,
they have remained autonomous, but there is also a manual
mode with controls from the ground.
|
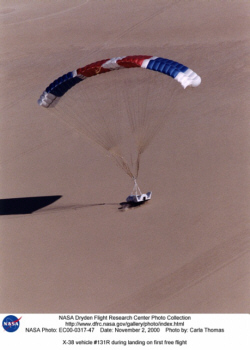
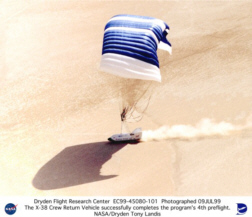
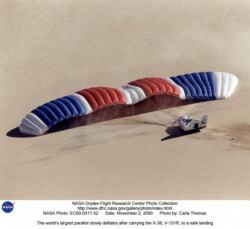 |